Supplier Audit
Level up your business with our audit squad!
ISO, IATF, VDA, ASPICE, AS/EN, ISO/IEC, BRC, PAS and the whole auditing crew can feel like a total drag, but they’re actually your secret weapon to crushing the competition.
We’ll show you how to turn those standards into serious strength.
Think of audits as power-ups for your business. They boost your rep, unlock new markets, and supercharge your efficiency. Our expert auditors are like pro gamers, navigating the complex rules to score you major points. Ready to dominate your industry? Let’s turn those standards into serious swag.
Systematize success, maximize revenue. Discover the power of your system.
Ready to take your business to the next level? System audit is your key to unlocking new opportunities.
We provide expert assessments of your system, products, and processes to ensure they meet the highest standards. Our audits validate your commitment to quality and excellence, building trust with customers and partners.
With a proven track record across diverse industries and complex regulatory environments, we’re your trusted partner in achieving organizational excellence.
Assessment process step by step
Your Toolbox for Success
Overview of 30 Types of Audits
We explore various types of audits, including system, human error, clinical, cybersecurity, and business continuity audits. Each audit plays a unique role in ensuring compliance, improving efficiency, and reducing risks.
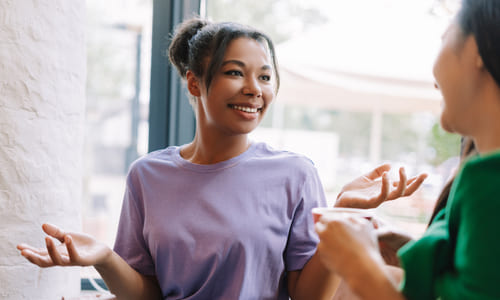
Our Success Stories
Your content goes here. Edit or remove this text inline or in the module Content settings. You can also style every aspect of this content in the module Design settings and even apply custom CSS to this text in the module Advanced settings.
Quality in the Supply Chain
Supplier audits are essential for ensuring quality, managing risks, and maintaining compliance in the supply chain. By conducting systematic evaluations of suppliers’ processes, products, and compliance with standards.
Product Safety and Security in the Global Supply Chain
Product safety and security in global supply chains face significant challenges due to their complexity, including risks of contamination, counterfeiting, and regulatory disparities. Industries such as food, pharmaceuticals, and medical devices are particularly vulnerable. Addressing these issues presents opportunities for research in regulation, traceability systems, and supplier management strategies. Read More..
Sustainability in Supply Chain Management
Sustainable supply chain management integrates environmental and social considerations into operations, reducing negative impacts while enhancing business performance. It involves tools like supplier codes, audits, and collaboration, with companies such as Unilever, Coca-Cola, and IKEA leading by example. This approach is vital for mitigating risks and achieving long-term profitability. Read more…
Frequently Asked Questions
What is a supplier audit?
A supplier audit is a comprehensive evaluation of a supplier’s operations, processes, and quality management systems to ensure they meet the agreed-upon standards, regulatory requirements, and contractual obligations. The audit assesses the supplier’s ability to consistently deliver products or services that meet the buyer’s expectations in terms of quality, reliability, and compliance.
Why are supplier audits important?
Supplier audits are important to ensure that suppliers adhere to quality, safety, and regulatory standards. They help minimize the risk of defects, delays, or non-compliant products entering the supply chain. Auditing suppliers ensures the reliability of their processes, fosters continuous improvement, and strengthens the buyer-supplier relationship by promoting transparency and accountability.
What are the types of supplier audits?
There are several types of supplier audits, including:
- Compliance audit: Ensures the supplier complies with regulatory, industry, or contractual standards.
- Process audit: Evaluates the supplier’s manufacturing or service processes to ensure consistency and control.
- Quality audit: Focuses on the supplier’s quality management system (e.g., ISO 9001) to confirm they have effective quality controls in place.
- Social responsibility audit: Assesses the supplier’s compliance with ethical, environmental, and labor standards, such as fair labor practices or sustainability initiatives.
What are the key steps in conducting a supplier audit?
The key steps in a supplier audit include:
- Audit Planning: Define the audit objectives, scope, and criteria. Schedule the audit with the supplier.
- Document Review: Assess supplier documentation such as quality policies, procedures, certifications, and past performance records.
- On-Site Audit: Visit the supplier’s facility to observe operations, review processes, interview staff, and inspect materials and products.
- Audit Report: Document audit findings, including any non-conformities, areas for improvement, and strengths.
- Corrective Action: Ensure the supplier addresses identified non-conformities with corrective actions and follow up on implementation.
What should be included in the scope of a supplier audit?
The scope of a supplier audit typically includes:
- Supplier’s quality management system: Ensure they follow appropriate quality controls and standards (e.g., ISO 9001).
- Manufacturing or service processes: Evaluate how products or services are produced or delivered.
- Supply chain management: Assess the supplier’s procurement, material handling, and logistics processes.
- Compliance with regulations and customer requirements: Ensure the supplier meets industry-specific standards (e.g., environmental or safety regulations).
- Workforce competency: Evaluate whether the supplier has skilled and trained staff to meet quality expectations.
How often should supplier audits be conducted?
The frequency of supplier audits depends on several factors, such as:
- Risk level: High-risk suppliers, such as those supplying critical components, may need more frequent audits (e.g., annually or semi-annually).
- Supplier performance: Suppliers with a history of non-conformities or quality issues may require more frequent audits.
- Industry or regulatory requirements: Some industries, such as pharmaceuticals or aerospace, may require regular audits to ensure compliance.
- Contractual obligations: Audit frequency may also be specified in contracts or agreements with the supplier.
Who should conduct a supplier audit?
Supplier audits are typically conducted by qualified personnel from the quality or procurement team, internal auditors, or third-party auditing firms with expertise in the relevant industry or process. Auditors should have knowledge of the supplier’s industry standards, regulatory requirements, and the specific product or service being supplied.
What are common findings in a supplier audit?
Common findings in supplier audits may include:
- Non-compliance with regulatory or contractual requirements.
- Inconsistent quality control measures or insufficient documentation.
- Lack of process standardization or inadequate process controls.
- Poor record-keeping or missing certifications.
- Insufficient workforce training or competence.
- Issues with material sourcing, traceability, or logistics.
- Non-conformities related to health, safety, or environmental standards.
How should a supplier respond to non-conformities found during an audit?
If non-conformities are identified during a supplier audit, the supplier should:
- Investigate the root cause: Perform a root cause analysis to identify why the non-conformity occurred.
- Implement corrective actions: Develop and implement corrective actions to address the issue and prevent recurrence.
- Communicate with the buyer: Provide timely updates on the corrective actions and demonstrate transparency.
- Follow-up monitoring: Continuously monitor the effectiveness of the corrective actions and ensure that they have resolved the issue.