ISO 9001 Clause: 4.2 Understanding the Needs & Expectations of Interested Parties
What are interested parties According to ISO 9001?
Interested parties are basically the key people or groups who receive your products or services, get impacted by them, or have a serious interest in what your company is up to.
Key Points: Just like reviewing the context of your organization, it’s crucial to get input from different teams. For example, procurement knows the suppliers best, while sales teams understand customers’ needs. Each team has its own connection to these stakeholders.
After you’ve figured out who your stakeholders are and what they expect, you need to check which of their requirements are tied to legal or compliance obligations for ISO standards. Focus on legal requirements first, before addressing other stakeholder needs.
Also, it’s important to make sure you’re regularly reviewing and updating these groups’ requirements, especially when you’re making changes to your QMS or when their needs evolve to keep up with ISO compliance.
ISO 9000 Quality management systems — Fundamentals and vocabulary
3.2.3 interested party, stakeholder
person or organization (3.2.1) that can affect, be affected by, or perceive itself to be affected by a decision or activity
EXAMPLE:Customers (3.2.4), owners, people in an organization, providers (3.2.5), bankers, regulators, unions, partners or society that can include competitors or opposing pressure groups.
Note 1 to entry: This constitutes one of the common terms and core definitions for ISO management system standards given in Annex SL of the Consolidated ISO Supplement to the ISO/IEC Directives, Part 1. The original definition has been modified by adding the Example.
Training Courses



What do you need to do to meet requirements?
To be compliant with Clause 4.2 of ISO 9001 here’s what you needs to do:
1. Identify Interested Parties
Determine who your stakeholders are, including: customers, suppliers, employees, regulators, investors, local communities, people or groups that have a significant impact on, or are impacted by, your products, services, or business operations.
2. Understand Their Needs and Expectations
Gather information about the specific needs, expectations, and requirements of these interested parties. This could involve: surveys or interviews with customers and suppliers, market research, industry analysis, regulatory requirements research. Understanding their needs helps ensure your Quality Management System (QMS) meets their expectations.
3. Determine Relevant Requirements
Figure out which of these stakeholder needs and expectations become mandatory requirements for your QMS. This includes: legal and regulatory obligations, compliance requirements, customer-specific requirements. Legal obligations take priority, but other stakeholder expectations also need to be factored into your system.
4. Monitor and Review Stakeholder Requirements
Set up a process to regularly review and update the needs and expectations of interested parties. This is especially important if:
- external factors change (new regulations, market shifts)
- the organization undergoes significant changes
- new stakeholders are identified
Stay proactive by continuously monitoring feedback and adapting to changes.
5. Communicate and Integrate Into QMS
Ensure that the relevant needs and expectations of interested parties are communicated across the organization and integrated into your QMS processes. This might include: customer feedback loops, supplier performance management, compliance with new laws or industry standards. Everyone within the organization should be aware of their roles in meeting these requirements.
By following these steps, you will align with Clause 4.2, ensuring that you understand and effectively address the needs and expectations of all key stakeholders as part of your ISO 9001 compliance.
Related Info
What are interested parties?
Interested parties in ISO 9001 are individuals or groups who have a vested interest in or are affected by your organization’s activities, products, or services. These parties can influence your business or be impacted by its outcomes.
Examples of interested parties
-
Customers – The organizations or individuals who purchase your products or services. They play a key role in driving revenue and shaping the overall demand for your offerings.
-
Users – The end-users of your product or service. They may not be the direct buyers but are the ones who interact with or consume the product. For example, a company (customer) might buy a product for its employees (users), and their experience can influence future purchases.
-
Distributors – These are intermediaries who buy your products and resell them to other customers or end-users. Distributors play a crucial role in your supply chain and market reach, helping you expand into new regions or market segments.
-
Suppliers – Companies or individuals providing essential goods, services, or resources that your organization depends on. Their quality and reliability directly affect your ability to meet your own quality standards.
-
Employees – Your internal workforce who directly contribute to your organization’s goals and performance. Their engagement and effectiveness impact productivity and the overall success of the business.
-
Regulators – Government agencies or industry bodies responsible for setting and enforcing legal, safety, and compliance standards that your organization must follow.
-
Shareholders/Investors – Individuals or groups with a financial interest in your business. They are concerned with profitability, growth, and how well the business is meeting its objectives.
-
Local Communities – The surrounding communities where your organization operates, especially if your activities have a direct impact on the environment, social conditions, or employment in the area.
-
Competitors – While not directly interacting with your organization, competitors affect market dynamics and can influence your strategic decisions.
-
Non-Governmental Organizations (NGOs) – Advocacy or watchdog groups with interests in specific areas like sustainability, social responsibility, or ethical business practices, which may interact with or influence your business.
How to understand needs and expectations?
ISO 9000 Quality management systems — Fundamentals and vocabulary
3.6.4 requirement
need or expectation that is stated, generally implied or obligatory
Note 1 to entry: “Generally implied” means that it is custom or common practice for the organization (3.2.1) and interested parties (3.2.3) that the need or expectation under consideration is implied.
Note 2 to entry: A specified requirement is one that is stated, for example in documented information (3.8.6).
Note 3 to entry: A qualifier can be used to denote a specific type of requirement, e.g. product (3.7.6) requirement, quality management (3.3.4) requirement, customer (3.2.4) requirement, quality requirement (3.6.5).
Note 4 to entry: Requirements can be generated by different interested parties or by the organization itself.
Note 5 to entry: It can be necessary for achieving high customer satisfaction (3.9.2) to fulfil an expectation of a customer even if it is neither stated nor generally implied or obligatory.
Note 6 to entry: This constitutes one of the common terms and core definitions for ISO management system standards given in Annex SL of the Consolidated ISO Supplement to the ISO/IEC Directives, Part 1. The original definition has been modified by adding Notes 3 to 5 to entry.
1. Identify Key Stakeholder Needs
Start by reviewing the needs and expectations you’ve gathered from customers, users, suppliers, distributors, employees, regulators, and other interested parties. Break these down into specific requirements—things that your organization must meet to satisfy them.
2. Categorize the Requirements
Organize the requirements into categories such as:
- Legal/Regulatory Requirements – Compliance obligations (e.g., safety regulations, data privacy laws).
- Customer Requirements – Quality, pricing, delivery expectations, and service standards.
- Internal Requirements – Employee needs like training, work environment, and tools for efficiency.
- Supplier/Distributor Requirements – Supply chain efficiency, contract terms, and communication expectations.
3. Prioritize Compliance and Legal Obligations
First and foremost, ensure you identify any legal and regulatory requirements. These are non-negotiable and must be met to avoid penalties or operational risks. This includes things like safety standards, environmental regulations, labor laws, and industry-specific compliance requirements.
4. Assess Mandatory vs. Voluntary Requirements
Determine which stakeholder expectations are mandatory (e.g., compliance requirements, contract terms) and which are voluntary (e.g., customer preferences for faster delivery, employee requests for additional benefits). While both are important, mandatory requirements take precedence.
5. Analyze Industry Standards
Compare your stakeholder expectations with industry standards. This can help you identify requirements that aren’t legally mandated but are critical for staying competitive, such as meeting certain product quality certifications (e.g., ISO standards) or sustainability benchmarks.
6. Review Contracts and Agreements
Go through any contracts, agreements, or SLAs (service-level agreements) with suppliers, customers, or partners. These documents often outline clear expectations and requirements that must be met as part of your business operations.
7. Consider Strategic Objectives
Align the relevant requirements with your organization’s strategic goals. For example, if you’re pursuing market leadership in sustainability, prioritize customer requirements for eco-friendly products or compliance with environmental regulations.
8. Use Risk Assessment Tools
Apply risk-based thinking to evaluate which requirements carry the most risk if unmet. Use tools like risk matrices to assess the potential impact and likelihood of failing to meet these requirements, which helps guide where you should focus your efforts.
9. Document the Requirements
Once you’ve identified and assessed the relevant requirements, document them clearly within your Quality Management System (QMS). This ensures that they are visible, trackable, and integrated into your processes.
10. Monitor and Update
Regularly review and update the list of relevant requirements as new laws are introduced, customer expectations evolve, or business priorities shift. Automated tools or reminders can help you stay on top of any changes.
By following these steps, you ensure that your organization identifies and addresses all relevant requirements from interested parties, keeping your business compliant, competitive, and aligned with stakeholder expectations.
Monitoring and Reviewing Stakeholder Requirements
1. Set a Regular Review Schedule
Establish a consistent schedule to review stakeholder requirements—whether it’s quarterly, semi-annually, or annually. This ensures you stay updated with any changes in needs or expectations from customers, users, suppliers, and other interested parties. Use tools like Google Calendar or Asana to set automated reminders for these reviews.
2. Track Changes in the External Environment
Keep an eye on external factors like market trends, industry shifts, new regulations, or economic changes. Use business intelligence tools like Power BI or Tableau to gather real-time data on these factors, helping you stay informed about evolving needs.
3. Engage with Stakeholders Regularly
Continuously communicate with your stakeholders (customers, suppliers, employees, regulators) through:
- Surveys or feedback forms to gauge customer satisfaction and identify emerging needs.
- Meetings or interviews with key partners or suppliers to understand their changing expectations.
- Focus groups or workshops to collaborate with cross-functional teams, ensuring all departments are in sync with stakeholder demands.
4. Use Performance Indicators (KPIs)
Set up KPIs to measure how well you’re meeting stakeholder requirements. For example:
- Customer satisfaction scores to track product or service quality.
- Supplier performance metrics to ensure timely deliveries and quality standards.
- Employee engagement surveys to monitor internal satisfaction and needs. Review these KPIs regularly to assess whether stakeholder requirements are being met.
5. Automate Monitoring with Software Tools
Use CRM systems like Salesforce or HubSpot to track customer interactions and feedback. These platforms can automatically record data on customer preferences, complaints, and requests, providing real-time insights into changing requirements.
6. Review Legal and Compliance Updates
Stay updated with any new legal or regulatory requirements that impact your business by subscribing to industry newsletters or using compliance management tools like VComply or ComplySci. This ensures that any legal obligations are tracked and incorporated into your reviews.
7. Create a Stakeholder Feedback Loop
Develop a feedback loop where you regularly gather input from stakeholders and act on it. For example, send out post-purchase surveys to customers or set up quarterly meetings with key suppliers to understand their evolving needs. This ensures ongoing engagement and real-time updates on expectations.
8. Involve Cross-Functional Teams
Engage different departments (e.g., sales, procurement, HR) in monitoring stakeholder requirements. Each department may have insights into the needs of specific stakeholders like customers or suppliers. Hold regular cross-functional meetings to ensure that these requirements are being tracked and addressed from all angles.
9. Document Changes and Updates
Ensure that all updates to stakeholder requirements are properly documented within your Quality Management System (QMS) and communicated across the organization. This helps keep everyone aligned and ensures that new requirements are integrated into business processes.
10. Adjust QMS as Necessary
Based on the findings from your reviews, update your QMS to ensure it continues to meet the latest stakeholder needs. This might involve revising certain processes, adjusting compliance measures, or setting new objectives to align with updated requirements.
By consistently monitoring and reviewing stakeholder requirements, you ensure that your organization stays aligned with their evolving needs, fostering stronger relationships and ensuring ongoing compliance with ISO 9001 standards.
Dive In
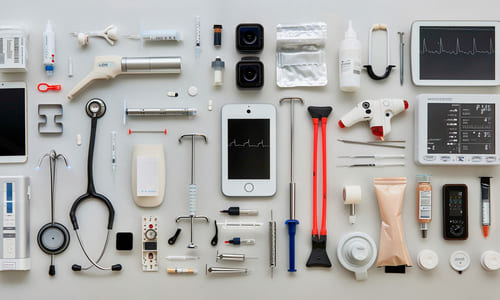
Ensuring Quality in Medical Devices: The Role of Process Validation and Revalidation
[dsm_gradient_text gradient_text="Ensuring Quality in Medical Devices: The Role of Process Validation and Revalidation" _builder_version="4.27.0" _module_preset="default" header_font="Questrial|||on|||||" header_text_align="center" header_letter_spacing="5px"...
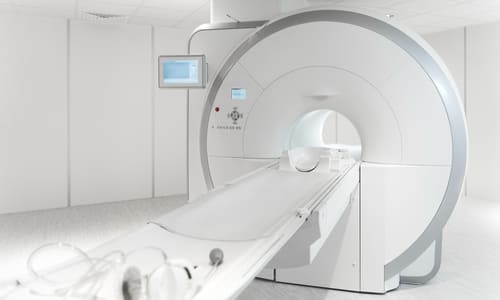
ISO 9001 vs. ISO 13485: Understanding the Similarities and Differences
[dsm_gradient_text gradient_text="ISO 9001 vs. ISO 13485: Understanding the Similarities and Differences" _builder_version="4.27.0" _module_preset="default" header_font="Questrial|||on|||||" header_text_align="center" header_letter_spacing="5px"...
How to Communicate and Integrate Into QMS?
1. Identify Key Stakeholders and Their Requirements
Before communicating or integrating anything, ensure you have a clear understanding of the key stakeholders (customers, suppliers, employees, etc.) and their specific needs. Prioritize legal, regulatory, and critical business requirements gathered from feedback, surveys, and market analysis.
2. Develop Clear Communication Channels
Set up defined communication channels across the organization to share stakeholder requirements. This could include:
- Internal newsletters or bulletins to keep everyone updated.
- Team meetings or department huddles to communicate specific stakeholder needs to relevant teams (e.g., sales, product development, procurement).
- Collaboration tools like Slack, Microsoft Teams, or Asana to provide updates in real-time and ensure all departments are aligned with the latest expectations.
3. Incorporate Requirements into Key Processes
Integrate the stakeholder requirements directly into the Quality Management System (QMS) processes by:
- Updating process documentation (SOPs, workflows, etc.) to reflect the new requirements.
- Ensuring project management tools like Trello or Monday.com are used to track the implementation of stakeholder needs in projects.
- Modifying quality control checklists to include critical stakeholder requirements (like customer-specific quality standards or legal regulations).
4. Train and Engage Employees
Ensure that employees understand the importance of meeting stakeholder requirements by offering training sessions and workshops. Use:
- E-learning platforms like Udemy or LinkedIn Learning to provide easy-to-access training on new standards and expectations.
- On-site or virtual workshops to explain the role of each team in meeting specific stakeholder needs.
- Regular Q&A sessions to clarify any concerns or confusions about stakeholder requirements.
5. Use a Documented Feedback System
Create a documented system for tracking, reviewing, and updating stakeholder requirements within your QMS. Tools like ISO document control software (e.g., Qualio or MasterControl) help you centralize and manage this information so it stays up-to-date and accessible to all relevant teams.
6. Align Stakeholder Needs with QMS Objectives
Align the stakeholder requirements with your QMS objectives and policies. Make sure key performance indicators (KPIs) reflect stakeholder expectations, such as:
- Customer satisfaction scores aligned with customer expectations.
- Supplier performance metrics related to timeliness and quality.
- Compliance checks tied to legal or regulatory obligations.
7. Regularly Communicate Updates
Use regular reports, dashboards, or meetings to keep teams informed of any updates to stakeholder needs and how they impact QMS processes. For example:
- Monthly reports summarizing new customer expectations or regulatory changes.
- Team huddles to discuss feedback from recent customer surveys or supplier performance reviews.
- Digital dashboards that track real-time feedback from stakeholders and how it’s being addressed in the QMS.
8. Monitor and Track Progress
Set up a system to monitor the progress of how well stakeholder requirements are being integrated and met within the QMS. Use:
- KPIs and metrics to track how well each department is addressing stakeholder needs.
- Internal audits to assess whether updated stakeholder requirements are being reflected in your processes and outcomes.
- Regular reviews of documentation and performance against stakeholder expectations to ensure ongoing compliance.
9. Encourage Cross-Department Collaboration
Ensure that departments collaborate effectively to address stakeholder needs. For example, sales teams need to communicate customer feedback to product development, while procurement should work with quality control to meet supplier requirements. Cross-functional teams or task forces can be created to address more complex or high-priority stakeholder needs.
10. Regularly Update the QMS Based on Stakeholder Changes
Stakeholder needs evolve, so it’s important to periodically review and update your QMS processes. Implement change management protocols to ensure that new stakeholder requirements are reflected in your QMS promptly and efficiently.
By following these steps, your organization can ensure that stakeholder requirements are effectively communicated and fully integrated into your QMS, keeping your operations aligned with ISO 9001 standards and ensuring that all parties’ needs are consistently met.
Conclusion
Clause 4.2 of ISO 9001 focuses on understanding the needs and expectations of interested parties, ensuring that your organization is aware of the stakeholders who can impact or be affected by your business. By identifying, monitoring, and addressing the requirements of these interested parties – such as customers, suppliers, employees, and regulators – your business can stay aligned with evolving expectations. This helps maintain compliance, improve customer satisfaction, and foster strong relationships with key stakeholders. Ultimately, this clause drives a proactive approach to integrating stakeholder needs into your Quality Management System (QMS), enhancing both operational efficiency and long-term success.
Wanna know more? Let's dive in!
New Zealand 2025
Duration: 2 weeks Cities: Christchurch, Hokitika, Kaikōura, Westport, Te Waipounamu, Nelson, Timaru Miles Travelled: 30 000Traveling through parts of New Zealand’s South Island offers a rich tapestry of history, landscape, and local character that leaves a quiet...
Resolving Die Peel Issues in an Automotive & Aerospace Electronics Manufacturing Plant
Background A global electronics manufacturer supplying critical components to the automotive and aerospace industries received multiple customer complaints regarding the premature failure of transistor-based power modules. Field analysis revealed that the root cause...
Transforming a Dysfunctional Quality Team in Automotive and Aerospace Manufacturing
Background The quality department of a Tier-1 manufacturer in the automotive and aerospace sectors was expected to ensure strict compliance to both customer and regulatory standards. Instead, it became a bottleneck plagued by poor collaboration, low morale, and high...
Resolving Customer Complaints Related to Electrical Connector Module Failures
Background ElectroTech, a manufacturer of electrical distribution components, including connector modules for power systems, received a major customer complaint regarding intermittent connection failures in one of its core electric product lines. The failures led to...
Singapore 2019
Duration: 3 days Cities: Singapore Miles Travelled: 6,300Visiting Singapore was like stepping into the future while still being surrounded by rich history and culture. From the moment I arrived at Changi Airport, with its indoor waterfalls and lush gardens, I knew...
Hawaii 2015
Duration: 2 weeks Cities: Honolulu Miles Travelled: 7,000Our trip to Hawaii was truly a once-in-a-lifetime experience, filled with breathtaking landscapes, warm hospitality, and unforgettable moments. We stayed in Honolulu on the island of Oahu, where the vibrant mix...
North East England 2024
Duration: 2 weeks Cities: Durham, Beamish Miles Travelled: 200Traveling to North East England offers a unique blend of history, culture, and character that stays with you long after you leave. One of the highlights is the enchanting city of Durham. Its cobbled streets...
Japan 2019
Duration: 2 weeks Cities: Osaka, Tokyo, Hiroshima, Kyoto Miles Travelled: 9,000Japan in spring is pure magic. Spring felt like a moment suspended in time. The cherry blossoms were at their peak, casting a soft pink glow over temple roofs and narrow cobblestone lanes....
Implementing ISO 18404 in Your Organization: A Practical Guide
[dsm_gradient_text gradient_text="Implementing ISO 18404 in Your Organization: A Practical Guide" _builder_version="4.27.0" _module_preset="default" header_font="Questrial|||on|||||" header_text_align="center" header_letter_spacing="5px" filter_hue_rotate="100deg"...
The Essential Skills and Knowledge Areas Covered by ISO 18404
[dsm_gradient_text gradient_text="Mastering ISO 18404: Essential Lean Six Sigma Competencies and Knowledge Areas" _builder_version="4.27.0" _module_preset="default" header_font="Questrial|||on|||||" header_text_align="center" header_letter_spacing="5px"...
The Future of Lean and Six Sigma
[dsm_gradient_text gradient_text="The Future of Lean and Six Sigma: How ISO 18404 is Shaping the Industry" _builder_version="4.27.0" _module_preset="default" header_font="Questrial|||on|||||" header_text_align="center" header_letter_spacing="5px"...
ISO 18404 vs. Other Lean and Six Sigma Certifications
[dsm_gradient_text gradient_text="ISO 18404 vs. Other Lean and Six Sigma Certifications: What's the Difference?" _builder_version="4.27.0" _module_preset="default" header_font="Questrial|||on|||||" header_text_align="center" header_letter_spacing="5px"...